Specification

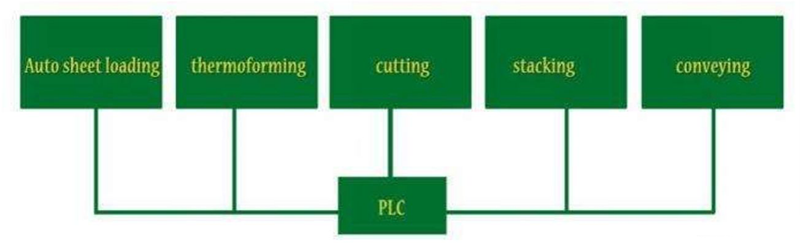
Main Features:
Adopt PLC control, the whole system is fully automatic, parameters digital
display, easy operation
This machine can produces plastic trays with sheets as per the date below x
being able to use various kinds of plastics sheets
4-pillar hydraulic structure, more stable, low noise
Imported heating wires ceramic heater, accurate temperature control, long life
We provide customized service for you, the machine can be designed and
manufactured as your need.
Advanced servo motor sheet transporting system, stretching length
Technical parameters:
|
|
HYX-7185-4
|
HYX-520
|
1
|
Suitable Material
|
PP, PS, PET, PVC, PLA, etc.
|
2
|
Material Width
|
450-740mm
|
3
|
Thickness of Material
|
0.15-2mm
|
4
|
Max. Forming Area
|
710×850mm
|
710×520mm
|
5
|
Min. Forming Area
|
420×300mm
|
6
|
Max. Cutting Area
|
690×830mm
|
690×500mm
|
7
|
Forming and Cutting Station Stroke
|
0-160mm
|
0-130mm
|
8
|
Positive Forming Depth
|
120mm
|
9
|
Negative Forming Depth
|
110mm
|
10
|
Stacking Mechanism Stroke
|
≤500mm
|
11
|
Maximum Force of molding
Station
|
80T (for use with die heating system)
|
60T (for use with die heating system)
|
12
|
Force maximum of cutting press
|
38 ton
|
35 ton
|
13
|
Rated Power of Heating Furnace
|
Upper oven 65KW, lower oven 65KW
|
Upper oven 45KW, lower oven 45KW
|
14
|
Heating Method
|
Upper and lower, 3 sections heating
|
15
|
Actual Energy Consumption
|
About 40~60KW/H About 30~50KW/H
|
16
|
Power Supply
|
AC 380V/50Hz (3+N+PE)
|
17
|
Max. Production Speed
|
20-30 cycles/minute
|
18
|
Max. Roll Diameter/Weight
|
Φ800mm/500KG
|
Φ700mm/300KG
|
19
|
Machine Weight
|
12,000kg
|
9,000kg
|
20
|
Dimension (L*W*H)
|
11m×2.3m×2.5m
|
9m×2.3m×2.5m
|
|
Cooling Method
|
The mold is cooled by circulating water
|
|
Air Request
|
Air supply ≥3.5m3/min, air pressure 0.6~0.8Mpa.
|
Main Configuration List
|
No.
|
Main electronic component
|
Brands
|
1
|
Control system
|
Taiwan Delta
|
2
|
PLC Module
|
Taiwan Delta
|
3
|
Touch screen
|
Delta 12 inch HD touch screen
|
Delta 10 inch HD touch screen
|
4
|
Temperature control system
|
Delta (Intelligent temperature control)
|
5
|
Intermediate relay
|
Schneider
|
6
|
AC Contactor
|
Schneider
|
7
|
Air switch
|
Delixi
|
8
|
Forming station servo motor
|
Delta(Upper: 5.5KW, Lower: 5.5KW)
|
Delta(Upper: 3KW, Lower: 3KW)
|
9
|
Cutting station servo motor
|
Delta(Upper: 7.5KW, Lower: 5.5KW)
|
Delta(Upper: 4.5KW, Lower: 3KW)
|
10
|
Punching station servo motor
|
Delta(Upper: 7.5KW,Lower: 7.5KW)
|
Delta(Upper: 4.5KW, Lower: 4.5KW)
|
11
|
Sheet delivering servo motor
|
Delta 5.5KW
|
Delta 3KW
|
12
|
Stacking servo motor
|
Delta 2KW with brake
|
13
|
Control cabinet
|
Shanghai Tong Ke
|
14
|
Photoelectric switch
|
Korea Fotek
|
15
|
Safety light curtain
|
Shanghai Pu Bang
|
16
|
Switching power supply
|
Taiwan Delta
|
17
|
Heating bricker
|
Joint venture imported heating wire, with thermal insulation cotton inside,600W far-infrared ceramic radiator
|
18
|
Vacuum pump
|
Elmo Rietschle V-VC100
|
19
|
Positive valve
|
Japan SMC ultra-high-speed response large-flow valve, with a diameter of 1.5 inches.
|
20
|
Cooling system
|
Japan Daikin Compressor 6P
|
21
|
Bearing
|
JAPAN NSK
|
22
|
Linear Guides
|
TAIWAN HIWIN
|
23
|
Hydraulic booster valve
|
JAPAN CKD
|
24
|
Air cylinder
|
TAIWAN AirTAC
|
25
|
Electromagnetic valve
|
JAPAN CKD/SMC
TAIWAN MINDMAN/SHAKO
|
26
|
Vacuum value
|
TAIWAN MINDMAN
|
27
|
Chain track
|
Aviation grade aluminum alloy
|
28
|
F.R.L
|
JAPAN CKD or SMC
|
29
|
Feeding system
|
Double-bar automatic mechanical feeding device to reduce the labor intensity of workers,500KG.
|
30 |
Body sheet metal
|
Paint treatment
|
31 |
Double-row chain
|
TAIWAN KMC
(Factory sharpening treatment reduces the occurrence of plastic powder.)
|
II. Device technical description
A. The forming equipment consists of the main structure frame, positive and negative pressure forming system, temperature control system, vacuum system,
heating system, air control system, electrical and PLC control system, punching system, product decomposition stacking and automatic rewinding system And
other structural components.
B. The main body of the equipment: It is made by welding and welding steel structural sections such as square and channel steel, which are used for assembly heating, die forming, die cutting and auxiliary devices. The overall steel structure frame is guided by <Structural Process Design>, and all the parts involved are fully in line with: high-quality material selection, blank production method, machining, heat treatment, parts assembly, machine operation, machine
maintenance and other process foundation to ensure that the movable device transmitting and transforming motion and force has sufficient strength and rigidity. All metal surfaces are treated with anti-rust treatment and the bottom layer is sprayed with anti-rust paint; general and standard parts are used in the structure to facilitate later maintenance and replacement of all parts.
Ⅲ. Electrical and PLC control systems/safety facilities
The electrical control system is controlled by a PLC-integrated module. The industrial touch display is used as the HMI (Human Machine Interface) and the
Chinese interface is used. The machine has buttons for operation and the setting and modification of all process parameters, making the equipment easy to operate and maintain.
The working method of the whole machine is divided into manual/automatic, all setting functions are operated on the touch display; after the operator has placed the materials, press the automatic startup equipment to complete the whole process of molding process until the material processing and production in the silo are completed; Manual is mainly used for mold change or sample control.
The system is equipped with multiple protection measures, and each action that may collide with each other is provided with interlocking and closed-loop control protection.
Safety door protective seal design, using manual buckle opening, manual locking, safety grating installed in the protection door to improve the safety factor of equipment and ensure the safety of personnel and property.
The distribution cabinet contains protection circuits, including overcurrent, overvoltage, undervoltage, short circuit, and overload protection. The heating element is protected by a fuse. For safety problems that may cause harm to the system or the workpiece, there are warning signs or remarks. 10% space is reserved in the control box for future changes. The electric cabinet is equipped with a filter and a protective cooling fan.
All non-removable cables and wires outside the power supply box are hidden in the cable slot for easy opening and repair. If this is not possible, use a hose to fix it.